The automotive industry is in the midst of a transformation. Industry 4.0 is rapidly becoming a reality throughout the sector, and the decarbonization megatrend is accelerated by digitization, new technologies, and the rise of e-mobility. Decarbonization impacts the entire sector's ecosystem: OEMs, suppliers, semi-finished products and raw materials, as well as recyclers, authorities, and ultimately, end customers.

Automakers have set themselves ambitious sustainability targets. To achieve net-zero carbon and help limit global warming to 1.5°C in line with the Paris Agreement, the industry, and its whole value chain must undergo significant changes. The key to success will be partnerships between businesses, consumers and governments, building ecosystems for sharing and reusing resources, working together to do more with less primary resources, less energy consumption, more renewable energy sources and thus less emissions. An inspiring vision for the automotive value chain that could mobilize all ecosystem participants is the idea of a zero-carbon and circular car: A vehicle that achieves its full potential with regard to carbon efficiency and circularity. It will require net-zero carbon emissions during the production and lifetime of the car and net-zero material waste at the end of its life. But how do we get there?
Market situation and outlook
During the last few years, decarbonization efforts in the automotive sector have focused mainly on the electrification of vehicles. Looking at the total greenhouse gas (GHG) emissions of a vehicle's lifecycle, the traditional powertrain is responsible for most of the emissions. It is also where automotive manufacturers have the most significant opportunity to positively influence compared to other GHG emitters such as material production or end-of-life materials recovery.
While electric vehicles (EV) account for only 7% of the world's passenger vehicle sales today according to McKinsey & Company, this is expected to change quickly in the next several years – accelerated by regulatory pressure paired with growing customer demand for more sustainable mobility. Statistics from European Automobile Manufacturers' Association (ACEA) show that battery electric vehicles (BEV) registration has more than doubled each year in Europe since 2019. According to McKinsey, by 2035, 100% of automotive sales in the largest markets (Europe, China, USA) are expected to be EVs, with premium players expected to electrify faster than volume players.
By 2035 100% of automotive sales in the largest markets are expected to be electric vehicles
The pathway to alternate powertrains includes new concepts and suitable energy storage systems, and related car body concepts. Car manufacturers are solving challenges such as integrating the battery most effectively, the importance of lightweight design, the resulting material concept, fulfillment of performance criteria, and creating sophisticated designs.
Aluminium, which is one of the most recycled materials on the planet, is ideal for lightweight designs across all vehicle segments. Its unique properties are perfectly suited to both the worldwide electromobility trend and the need for the automotive industry to decarbonize. With up to 42% weight reduction compared to steel with comparable or better performance, aluminium is increasingly becoming the material of choice for safe, cost-effective, and sustainable bodywork construction. As the leading producer of flat-rolled aluminium products and the world's largest recycler of aluminium, Novelis partners with most of the world's largest OEMs to develop innovative lightweight solutions for the growing demands of the automotive sector. "Our commitment to sustainability is core to our business operations and extends to how we work with stakeholders across the aluminium value chain. We see tremendous opportunities in expanding the use of lightweight, infinitely recyclable aluminium to help OEMs achieve their sustainability goals and provide consumers with the low carbon products they enjoy," says Michael Hahne, Vice President Automotive Europe at Novelis.
Decarbonizing all three phases in a car's lifecycle
Electrification of Use Phase
Studies show that fuel and exhaust make up 65 - 80% of a car's emissions during its lifetime; the phaseout of internal combustion engine vehicles (ICEV) and the shift towards electric powertrain technology seems logical and essential.
Many countries have reinforced the adoption of EVs with respective regulations and plan to ban internal combustion powertrains in the long run. One of the earliest adopters in combating climate change, Norway has announced a sales ban for ICEVs as early as 2025, with several European countries following by 2030. Consequently, the majority of OEMs have announced an end date for petrol and diesel engines, and the switch to electromobility is in high gear. Electromobility must be accompanied by a shift towards renewable energy and new business models for charging. For example, in China, the biggest BEV market, different battery swapping services are being pioneered. The development of electromobility and, in parallel, the shift to a circular economy can revolutionize the way cars are manufactured and used.
With a high adoption of electric vehicles underway, the share of a car's lifetime emissions shifts from the use phase to production and end-of-life.
With a high adoption of EVs underway, the share of a car's lifetime emissions shifts from the use phase to production and end-of-life. Embedded material emissions will dominate vehicle lifecycle emissions, up to 60%, once a car is no longer powered by fuel. It therefore becomes clear that it will take more than phasing out ICEVs to reduce carbon emissions drastically.

Circularity in the production phase
In the circular economy, raw materials and goods are designed, built, repaired, and reused so that, as far as possible, there is no more waste in the conventional sense, but the raw materials remain within a closed loop. The car should not be scrap at the end of its life but a "material bank" for new vehicles.
While we are still far away from cars becoming a source of valuable materials at the end of their lives, initiatives to close the loop during the production phase are ongoing. For example, Novelis has implemented highly developed closed-loop recycling systems in cooperation with many of its automotive customers. This enables customers to return the aluminium scrap generated during the car manufacturing process directly back to Novelis for recycling into products of similarly high value, without any loss of quality. The closed-loop recycling system reduces the need for primary aluminium, thereby reducing energy use and carbon emissions, as recycling aluminium requires only 5% of the energy needed for producing primary aluminium.
Novelis combines this closed-loop recycling with more sustainable logistics, thanks to the ever-increasing shift in the transportation of aluminium sheet from road to rail. CO2 emissions during transport are thus reduced by up to 70%, and in individual cases by as much as 90%.

On its journey to carbon neutrality, Novelis is also researching options for decarbonizing the melting process and capturing the carbon produced during secondary aluminium production.
To reach carbon neutrality in the production phase, the sourcing of renewable energy is key. Increasing the availability and stability of renewable energy supply is an ongoing objective for the entire industry. Reducing the overall energy intensity by implementing new and less energy-intensive processes and technologies is also crucial. But reducing energy consumption and the ongoing shift to renewable energy alone will not be sufficient to decarbonize the lifecycle of vehicles. Circular business models are required to reduce emissions from manufacturing. Closing the recycling loop during production is the first level in the current system. In the very near future, designing a car for recycling and building a framework that enables the retrieval of the materials and their return to the recycling loop at the end of the vehicle's life are the next necessary steps.
Bringing cars back into the loop at the end of their life
Especially with a material like aluminium, which is infinitely recyclable, a framework that enables and incentivizes circular product systems is key for decarbonization: a system where the products having reached the end of their useful life are recycled into the same products, again and again.
"The materials which can be recycled into high-value products again, like aluminium, must be dismantled, collected, and sorted in a way that preserves their value so that they can start their life again in a new car. Design for recycling and re-manufacturing is going to be an entire area of development in the partnerships with OEMs and other industry partners so that together we can create the same success story we have built up together with them on the closed-loop model for production scrap," explains Michael Hahne.
In many countries, recycling systems are already well established and efficient for products such as the aluminium beverage can, which, once consumed, can be thrown into a recycling bin, and from there, it starts its journey to be transformed into a new can in as little as 60 days. In comparison, the car is a highly complex product, with more than 1,000 materials in a single-vehicle. The automotive value chain must innovate and partner across sectors to find solutions that will allow the multitude of materials present in a vehicle at the end of its life to be recycled into products that will again be used in the production of new vehicles.
End-of-life should already be considered in the vehicle design – to make recycling efficient and reduce the need for virgin inputs
For the aluminium built into a car to be recycled efficiently, a few factors have to be considered. The focus is undoubtedly on developing new concepts and business models to efficiently capture incorporated materials at the end of the product lifecycle. End-of-life should already be considered in the vehicle design – to make recycling efficient and reduce the need for virgin inputs. Novelis also aims to continue increasing the recycled content of its products. The company works with their customers and industry partners already at the design stage of new products and takes the dismantling process at the end of a product's life into account, making it easier for the materials to be collected, sorted, and recycled.
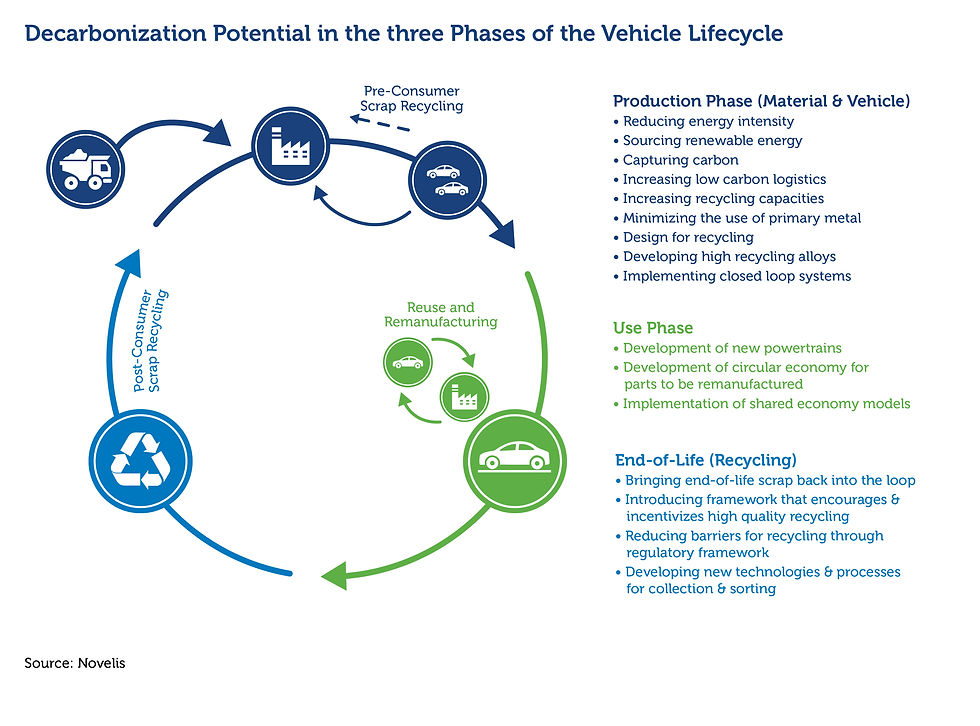
Efficient dismantling capability is another key aspect. For secondary materials to compete in the marketplace, the vehicle and individual components must be dismantled quickly and cost-effectively. The prerequisites for this also have to be put in place when designing the vehicle – for example, by not securing connections with adhesive, but designing them so that they can be detached again efficiently at the end of the vehicle life and ensuring different materials are not mixed.
Consumers and regulators can also accelerate the change for the enhanced collection, sorting, and recycling of end-of-life scrap by requesting traceability of the remainder of a vehicle at the end of its life. Extracting components and materials and bringing them back into the loop will be a game-changer for the environment. As an advocate for this, Novelis promotes public awareness on recycling and the development of new concepts and technologies, especially in the digitalization sector.
New technologies will enable traceability and reinforce the circular economy
The automotive industry's complex value chain means that customers – and not even OEMs themselves - have complete and consistent visibility into the sources of the industry's emissions. "One key to success in decarbonization is to be found more than ever in establishing partnerships and in 'simultaneous engineering.' It's not only about innovative, circular, and efficient products and solutions but also about establishing new business and cooperation models and a new dimension of digitalization and transparency within the industry. Developing a comprehensive approach to traceability of material emissions for industry players and customers would greatly facilitate decarbonization," says Michael Hahne. Approaches to this exist, and Novelis is currently part of a pilot project to track materials across all parties involved - starting from material producers to the final product.
New technologies such as smart contracts based on blockchains can make the circular economy a reality as they allow for the exchange of data, e.g. on CO2/t, without sharing (sensitive and proprietary) material composition information. It also makes collaboration with suppliers, waste management companies, service providers and new players so easy that a transparent, circular ecosystem can exist. This can create closer and more lasting ties between partners and help tackle the existing issue of not bringing back a majority of a car's material to a similar high quality at the end of its life.
The fourth industrial revolution could overturn the principle that the production of goods always leads to the production of waste. Each part will become traceable with a digital product ID, making it possible to replace the traditional concept of "take - make - waste" with "rethink - reuse - recycle."
Conclusion
EVs play a central role in the automotive industry's ambitious objective of zero emission targets set for 2050, but it is time to look beyond the electrification of the vehicle's use phase. The industry will only achieve its climate targets by making fundamental changes in all three phases of a vehicle's lifecycle and moving towards a fully circular economy. To make the zero-carbon car a reality, efforts must now focus on all levers the industry can pull. Especially closing the loop at the end-of-life will only be possible if all automotive ecosystem players work together and cooperate in unprecedented ways.
While the circular economy can revolutionize the industry much like Henry Ford's assembly line once did, it depends on technological, environmental, economic, political, and social dimensions that we all have to shape.
Further information:
Novelis is a global leader in producing innovative aluminium products and solutions and the world's largest recycler of aluminium. In the last ten years, Novelis invested $700M USD and increased the percentage of recycled content on average across all products from 33 in 2010 to 61% to date. Their ambition is to be the leading provider of low-carbon, sustainable aluminium solutions and achieve a fully circular economy by partnering with their suppliers and customers worldwide.
Comments